Search Blogs
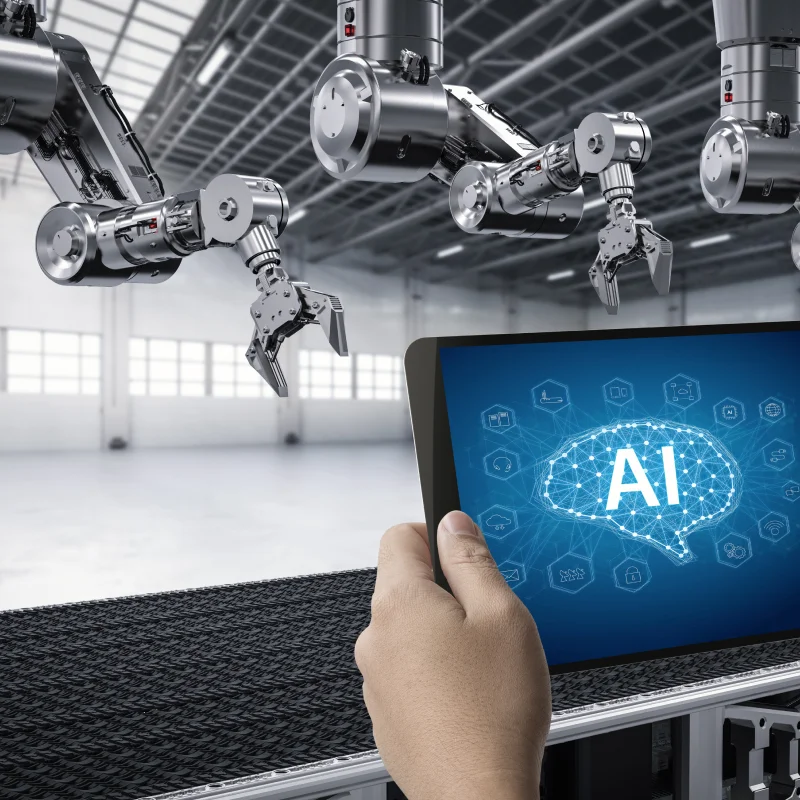
How AI is Revolutionizing Manufacturing Efficiency in 2024
Artificial intelligence (AI) has been a buzzword for decades, but it's only in recent years that we've truly begun to unlock its transformative potential across industries. From healthcare to finance, transportation to entertainment, AI is proving to be a game-changer, and the manufacturing sector is no exception. As we navigate through 2024, AI's impact on manufacturing efficiency is nothing short of revolutionary.For years, manufacturers have grappled with the challenges of optimizing production processes, reducing waste, and maximizing output while minimizing costs. Traditional methods often fell short, leading to inefficiencies, quality control issues, and missed opportunities. However, with the advent of advanced AI technologies, manufacturers are now poised to overcome these hurdles and embrace a new era of unprecedented efficiency.This blog post will delve into the ways AI is revolutionizing manufacturing efficiency in 2024, highlighting key areas where this transformative technology is making a significant impact, from predictive maintenance and quality control to production planning and collaborative robotics. We'll explore real-world examples, innovative solutions, and the potential for even greater advancements in the years to come.Predictive Maintenance: Proactive, Data-Driven Equipment CareOne of the most profound ways AI is optimizing manufacturing efficiency is through predictive maintenance. In the past, maintenance schedules were often based on guesswork or rigid timelines, leading to unnecessary downtime and costly repairs. However, with AI's ability to analyze vast amounts of sensor data from machines, manufacturers can now predict failures before they occur, allowing them to schedule maintenance proactively and minimize disruptions to production.AI algorithms can detect subtle patterns and anomalies in sensor data that might indicate an impending issue, such as abnormal vibrations, temperature fluctuations, or changes in power consumption. By continuously monitoring these signals, AI systems can alert maintenance teams to potential problems, enabling them to take corrective action before a breakdown occurs.The benefits of predictive maintenance are manifold. Firstly, it significantly reduces unplanned downtime, which can be incredibly costly for manufacturers. According to a report by Vanson Bourne, unplanned downtime costs industrial manufacturers an estimated $50 billion annually. By catching issues early, manufacturers can minimize disruptions and keep their production lines running smoothly.Secondly, predictive maintenance extends the lifespan of equipment, reducing the need for premature replacements and saving companies substantial capital expenditures. A study by the U.S. Department of Energy found that predictive maintenance can lead to a 25-30% reduction in maintenance costs and a 70-75% decrease in breakdowns.Thirdly, by optimizing maintenance schedules, manufacturers can better allocate their resources, reducing labor costs and increasing overall efficiency.Companies across various manufacturing sectors are already embracing AI-powered predictive maintenance solutions. For example, Siemens, a global industrial manufacturing company, has implemented a predictive maintenance system called "Siemens Siebert" in its production facilities. This AI-powered system analyzes data from sensors on machines to predict when maintenance will be required, reducing unplanned downtime by up to 25%.Similarly, Bosch, a leading manufacturer of automotive components and consumer goods, has developed an AI-based predictive maintenance solution called "Bosch Predictive Maintenance Services." This system uses machine learning algorithms to analyze data from connected devices and equipment, enabling Bosch to optimize maintenance schedules and reduce unplanned downtime by up to 30%.AI-powered Quality Control: Ensuring Product ExcellenceAnother area where AI is revolutionizing manufacturing efficiency is in quality control. Traditionally, quality inspections have relied heavily on human inspectors, who can be prone to fatigue, inconsistency, and subjective biases. However, AI-powered vision systems and machine learning algorithms are now enabling manufacturers to inspect products with unparalleled accuracy, speed, and consistency.These AI-based quality control systems use advanced computer vision and deep learning techniques to analyze images or videos of products as they move along the production line. By training these algorithms on vast datasets of defective and non-defective products, AI systems can quickly and accurately identify even the slightest imperfections, such as cracks, scratches, discolorations, or dimensional inaccuracies.The benefits of AI-powered quality control are substantial. Firstly, it leads to a significant reduction in defective products, minimizing waste and ensuring consistently high levels of quality. According to a report by Capgemini, AI-based visual inspection systems can reduce defect rates by up to 90%.Secondly, by automating the inspection process, manufacturers can significantly increase the speed and throughput of their quality control operations, improving overall efficiency and reducing bottlenecks.Thirdly, AI-based quality control systems can provide valuable insights and data analytics, enabling manufacturers to identify the root causes of defects and continuously improve their processes.Several companies have already implemented AI-powered quality control solutions with impressive results. For example, Foxconn, a major electronics manufacturer, has deployed an AI-based visual inspection system in its production facilities. This system can inspect products at a rate of 30 items per minute, with an accuracy rate of 99.9%. By automating the inspection process, Foxconn has reduced its defect rate by 80% while increasing its production capacity.Another example is BMW, the German automotive giant. BMW has implemented an AI-powered quality control system in its manufacturing plants, using computer vision and machine learning algorithms to inspect vehicle bodies for defects. This system is capable of inspecting a car body in just 60 seconds, with an accuracy rate of 99.9%. By automating this process, BMW has significantly improved its quality control efficiency while reducing the risk of human error.Optimized Production Planning and Scheduling: Maximizing EfficiencyBeyond predictive maintenance and quality control, AI is also revolutionizing manufacturing efficiency through optimized production planning and scheduling. In today's dynamic and complex manufacturing environments, effectively managing production schedules, resource allocation, and inventory levels is a monumental challenge. However, AI's ability to process vast amounts of data and identify intricate patterns is enabling manufacturers to optimize these processes like never before.AI algorithms can analyze historical production data, real-time machine data, demand forecasts, supplier lead times, and a myriad of other factors to develop highly optimized production schedules. These schedules take into account resource constraints, such as machine availability, labor availability, and raw material inventory, to ensure that production runs as efficiently as possible.By optimizing production schedules, manufacturers can reduce lead times, increase production capacity, minimize resource waste, and respond more quickly to changing customer demands or market conditions.Additionally, AI can optimize inventory management by analyzing demand patterns, supplier performance, and production schedules to ensure that the right materials and components are available when needed, without excessive overstocking or stockouts.Companies across various industries are leveraging AI for optimized production planning and scheduling. For example, Intel, the world's largest semiconductor manufacturer, has implemented an AI-powered production planning system called "Lean Manufacturing Analytics." This system analyzes data from Intel's factories and supply chain to optimize production schedules, reducing cycle times by up to 25% and improving on-time delivery rates by 16%.Another example is Procter & Gamble (P&G), the consumer goods giant. P&G has developed an AI-based supply chain optimization system called "Demand Orchestration." This system uses machine learning algorithms to analyze data from multiple sources, including sales forecasts, inventory levels, and transportation logistics, to optimize production schedules and inventory management across P&G's global operations. By implementing this system, P&G has reduced inventory levels by 10% while improving service levels and on-time deliveries.Collaborative Robots (Cobots): Enhancing Human-Machine CollaborationWhile AI is automating and optimizing many manufacturing processes, it's also enabling a new era of human-machine collaboration through the use of collaborative robots, or cobots. These AI-powered robots are designed to work alongside humans on the factory floor, performing tasks safely and efficiently while leveraging the unique strengths of both human workers and robotic systems.Cobots are equipped with advanced sensors, computer vision, and machine learning algorithms that allow them to perceive their surroundings, anticipate human movements, and adapt their behavior accordingly. This ensures a safe and seamless collaboration between humans and robots, minimizing the risk of accidents or disruptions.By augmenting human workers with cobot assistants, manufacturers can significantly increase productivity and efficiency. Cobots can handle repetitive, physically demanding, or hazardous tasks, freeing up human workers to focus on more complex, value-adding activities.Moreover, cobots can be easily programmed and redeployed for different tasks, providing manufacturers with greater flexibility and agility to respond to changing production requirements or product designs.The benefits of cobots extend beyond productivity gains. By automating physically demanding tasks, cobots can reduce the risk of workplace injuries and improve overall worker safety. Additionally, cobots can help address labor shortages in certain manufacturing sectors by supplementing the human workforce and reducing the need for additional hiring.Companies across various industries are embracing cobots to enhance efficiency and productivity. For example, Ford Motor Company has implemented cobots in its manufacturing facilities to assist human workers with tasks such as material handling, machine tending, and assembly. By deploying these cobots, Ford has increased production efficiency by up to 30% while improving worker safety and ergonomics.Another example is Siemens, which has implemented cobots in its electronics manufacturing plants. These cobots work alongside human workers to perform tasks such as circuit board assembly, component placement, and quality inspection. By leveraging the strengths of both humans and cobots, Siemens has improved production efficiency, reduced errors, and enhanced overall quality.SummaryAs we navigate through 2024, it's clear that AI is revolutionizing manufacturing efficiency in unprecedented ways. From predictive maintenance and quality control to optimized production planning and collaborative robotics, AI is enabling manufacturers to overcome longstanding challenges and unlock new levels of productivity, quality, and cost-effectiveness.The examples and case studies highlighted in this blog post are just the tip of the iceberg. As AI technologies continue to advance and manufacturers become more adept at leveraging these solutions, the impact on efficiency is likely to grow even more profound.However, it's essential to acknowledge that while AI is a powerful tool, it's not a panacea. The successful implementation and adoption of AI in manufacturing require a careful balance of technology, process optimization, and workforce enablement. Manufacturers must invest in upskilling and reskilling their workforce to ensure that human workers can effectively collaborate with AI systems and embrace the transformative changes brought about by these technologies.Furthermore, concerns about job displacement and workforce disruption must be addressed proactively. While AI and automation may lead to the elimination of certain roles, they also create new opportunities for skilled workers in areas such as data analysis, AI development, and process optimization. By focusing on workforce enablement and continuous learning, manufacturers can navigate this transition successfully while maintaining a skilled and engaged workforce.Looking ahead, the future of manufacturing efficiency lies in the seamless integration of AI, automation, and human expertise. By leveraging the strengths of both artificial and human intelligence, manufacturers can unlock new levels of efficiency, agility, and competitiveness in an ever-evolving global marketplace.If you're a manufacturer looking to stay ahead of the curve, now is the time to explore how AI can revolutionize your operations. Invest in AI skills and resources, pilot AI solutions in your facilities, and embrace a culture of continuous learning and innovation. The future of manufacturing efficiency is here, and those who harness the power of AI will be well-positioned to thrive in the years to come.Adoption of AI TechnologyWhile this blog post has focused on the core areas of predictive maintenance, quality control, production planning, and collaborative robotics, it's important to note that AI's impact on manufacturing efficiency extends far beyond these applications.For instance, AI is playing a vital role in demand forecasting, enabling manufacturers to more accurately predict future demand patterns based on historical data, market trends, and a multitude of other factors. By optimizing production levels to match demand, manufacturers can minimize excess inventory, reduce waste, and improve overall efficiency.Additionally, AI is being leveraged for personalized product design and mass customization. By analyzing customer data and preferences, AI algorithms can assist in designing products tailored to specific customer segments or even individual customers. This not only enhances customer satisfaction but also streamlines the manufacturing process by reducing the need for excessive product variations and complexity.Another area where AI is making an impact is energy optimization. AI systems can analyze energy consumption patterns, production schedules, and environmental factors to optimize energy usage, reduce waste, and minimize the environmental footprint of manufacturing operations.While the potential benefits of AI in manufacturing are vast, it's essential to address the concerns surrounding job displacement and workforce disruption. As AI automates certain tasks and processes, there is a valid concern that some manufacturing jobs may become obsolete or transformed.However, it's crucial to recognize that AI is not inherently a job-killer; rather, it's a tool that can augment and enhance human capabilities. The key is to focus on upskilling and reskilling the workforce to adapt to the changing landscape of manufacturing. By investing in training programs, workforce development initiatives, and continuous learning opportunities, manufacturers can ensure that their employees are equipped with the skills necessary to collaborate with AI systems and thrive in the era of intelligent automation.Moreover, the adoption of AI in manufacturing is likely to create new job opportunities in areas such as data analysis, AI development, process optimization, and system integration. As manufacturers embrace these technologies, there will be a growing demand for skilled professionals who can design, implement, and maintain AI systems, as well as interpret the data and insights generated by these systems.To support this transition, manufacturers must foster a culture of lifelong learning and encourage their employees to continuously develop new skills and competencies. By creating an environment that values continuous improvement and embraces change, manufacturers can ensure that their workforce remains relevant and valuable as AI technologies continue to evolve.In addition to addressing workforce concerns, it's also essential for manufacturers to prioritize responsible and ethical AI practices. As AI systems become more prevalent in manufacturing operations, it's crucial to ensure that these systems are transparent, accountable, and aligned with ethical principles and societal values.This includes addressing issues such as data privacy, algorithmic bias, and the potential for AI systems to perpetuate or amplify existing biases or discrimination. Manufacturers must implement robust governance frameworks, ethical guidelines, and auditing processes to ensure that their AI systems are operating in a fair, transparent, and responsible manner.By addressing these concerns proactively and fostering a culture of responsible AI adoption, manufacturers can mitigate potential risks and build trust with their customers, employees, and stakeholders.In conclusion, the impact of AI on manufacturing efficiency in 2024 is truly revolutionary. From predictive maintenance and quality control to optimized production planning and collaborative robotics, AI is enabling manufacturers to overcome longstanding challenges and unlock new levels of productivity, quality, and cost-effectiveness.However, the successful adoption of AI in manufacturing requires a holistic approach that balances technology, process optimization, workforce enablement, and responsible AI practices. By embracing these principles and continuously innovating, manufacturers can harness the full potential of AI and position themselves at the forefront of the Fourth Industrial Revolution.At RWaltz, we pride ourselves on pioneering innovative solutions tailored for esteemed Fortune 500 companies, leveraging state-of-the-art AI and other leading-edge technologies. Our commitment to excellence has enabled us to deliver transformative outcomes across diverse industries.I am pleased to share an insightful article showcasing our groundbreaking work, which I believe could greatly benefit your esteemed firm. Should you find the content pertinent to your objectives, I invite you to schedule a consultation with our team. Together, we can explore the potential implementation of similar solutions tailored to your unique requirements.To learn more about our offerings and to schedule a discussion, please visit our website www.rwaltz.com.
Let's Build Your Vision Together
Get Started with RWaltz Today!